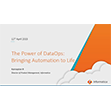
How Coke Bottlers Save Millions with AI
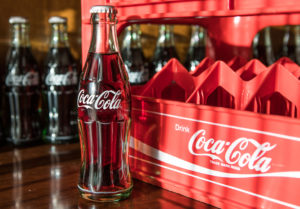
(MAHATHIR MOHD YASIN/Shutterstock)
Retailers around the country rely on a network of nearly 70 independent Coca-Cola bottlers to manufacture and ship cases of liquid refreshments. It’s a finely tuned supply chain, and it ultimately serves customers well. But getting a consolidated view into the millions of paper-based billing and shipping documents was a major headache for the network–that is, until an innovative use of computer vision and NLP technology helped digitize it.
Starting around 2007, Coca-Cola North America worked to “refranchise” its bottling and shipping operations, which spans 51 production facilities, 350 distribution centers, and involves more than 55,000 employees. The company says the goal of this refranchising effort is to “bring the heart of Coca-Cola back to the local bottler,” which in some cases are multi-generational companies more than 100 year’s old.
A key player in all this is the Coca-Cola Bottler’s Sales and Services Company. Founded in 2003, CCBSS is a shared service provider that is jointly owned by the nearly 70 independent Coca-Cola bottlers that make and move products under license with Coca-Cola North America. CCBSS’ goal is to be a unifying force for the bottlers and to enable them to act as one. But there are some major caveats to that unity.
While there are some common IT systems in place to automate business processes, the individual bottlers each have their own systems and processes in place, and they are not uniform. CCBSS relies on ERP software from SAP to automate its business processes, but the various member companies are free to use whatever systems they want to handle accounts receivable and accounts paying (AR/AP) systems.
Instead of forcing standardized systems, CCBSS has tried to stitch together the processes and systems as best they can after the fact. In many cases, this means falling back on the lowest common denominator: paper-based forms.
Until recently, CCBSS has relied on a network of outside service providers to reconcile approximately 230,000 paper-based documents generated every week. FedEx moved the documents. Iron Mountain stored the paper and did some processing. Xerox-spinoff Conduent supplied the optical character recognition (OCR) for digitizing the documents. OnBase by Hyland provided the workflow automation. And exception handling and manual data entry was handled by Capgemini India.
But the company hit a limit in terms of the volume of documents it could process, and the efficiencies that could come out of it. That’s when CCBSS started looking for alternative, which is what ultimately brought it to a Hayward, California company called Ripcord.
Ripcord bills itself as the world’s first “robotic digitization company.” The company’s capabilities span from, robotic process automation (RPA), including high-speed document sorting and scanning machines, to using deep learning approaches through computer vision and NLP.
When CCBSS approached Ripcord for a possible business engagement, the possibility looked fruitful off the bat, according to Ripcord co-founder and CTO Kevin Hall.
“When we started talking to them, we realized that we could basically consolidate all of these vendors into one service offering through Ripcord,” Hall tells Datanami. “We handle everything, from the receiving the mail, processing it, using software now to extract the data and connecting it into, ultimately, SAP.”
The start of the workflow remains unchanged. When a delivery driver completes her delivery, she will often print out a proof of delivery document, which is often paired with an invoice that is also in paper form. At the end of the day, the drivers bring all of those proof-of-delivery documents and invoices back, pile them up, and mail them to a central site to be processed and connected into SAP, according to Hall.
You might be thinking: Why doesn’t CCBSS just have their drivers use a bunch of iPads? Well, it’s not that simple. They do use iPads for some functions, but a migration en masse to handhelds is not feasible. Having Coke dictate exactly how nearly 70 supposedly independent companies must run their businesses goes against the whole point of having independent bottlers.
“Because it’s such a distributed and large number of bottlers, that’s somewhat why they’ve stuck to paper, because it’s like this common denominator of data transfer,” Hall says.
CCBSS signed on with Ripcord to bring more automation to its workflow using the vendor’s hosted workflow system, called Canopy. According to Hall, the workflow hasn’t greatly changed under Canopy. The data still starts out on paper, and ultimately ends up in SAP. But improvements made to the various steps in between have improved dramatically.
With the new process, CCBSS bottlers mail their documents to Ripcord’s processing facility in Hayward, where a robot created by Ripcord sorts through the documents, looks for staples (which have to be removed) and does the initial OCR scan. The machine employs a novel computer vision model created by Ripcord that’s able to classify documents based on their appearance.
According to Hall, the AI in the sorting machine is able to eliminates much of the manual work that previously was required to set up the OCR system, particularly around bundling the documents and using barcodes to identify them.
“A lot of times, the documents come bundled, so they were pre-prepped at the branch in a meticulous way,” Hall says. “We’ve been able to work with them to say, hey you don’t actually need to be that meticulous, because our document matching algorithms are able to look at the related documents and key off of invoice number, for example, and tie them together.”
Once the documents have been identified and scanned, Ripcord’s Canopy system uses NLP models to extract data from relevant fields on the documents, and map the data into the key-value pairs that ultimately are loaded into CCBSS’s SAP system. The accuracy on this data extraction process (which can also use barcodes if they’re available) has increased by 50%, according to Hall.
All told, the vendor consolidation enabled by Canopy is saving CCBSS $1 million per year, according to Ripcord. But the savings are likely much higher. Because Ripcord is running at a 99.95% accuracy level, it has streamlined the exception-handling processes that CCBSS previously had to retain for the 1 million shipping and billing documents it was processing per month.
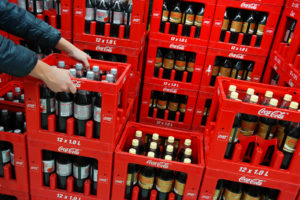
The diversity of bottlers means paper-based invoices remain a core element of CCBSS’ operations (defotoberg/Shutterstock)
“There are definitely people at Coke who had the job of going through and helping clean up that backlog,” Hall says. The backlog now is “near zero. I’m sure some things enter the backlog every now and again, but we’re able to basically bring that down to nothing for them.”
Because the backlog has been eliminated, CCBSS is able to take action to resolve invoice disputes much more quickly. Before, if a dispute arose on an invoice that was associated with a backlogged document, the bottling network may have opted not to contest it and give the independent bottler what it wanted. But with better data, the company can now fight those disputes, which Hall says is likely saving CCPSS millions.
According to Hall, emerging AI techniques have the potential to revolutionize document classification and workflow issues, and save customers large sums of money as they transition themselves all digital workflows. The company has been lucky to work with large companies, such as CCBSS, Mitsubishi Union Bank of Japan, Bechtel, and others, which seeds its deep learning systems with lots of data.
“Our general models over time are getting better and better at document classification, and they’ll be at a point where we can onboard a new customer and our out-of-the-box models are going to work perfectly for their HR use case, for example,” Hall says. “We think that paper has been a bit of that anchor holding companies back, so if we can digitize it and help them realize that future than where we’ve done our job well.”
Related Items:
SAP Seeks RPA Bot Breakthrough, But Will Workflows Cooperate?
How AI Boosts Human Expertise at Wolters Kluwer
Deep Learning Is Great, But Use Cases Remain Narrow